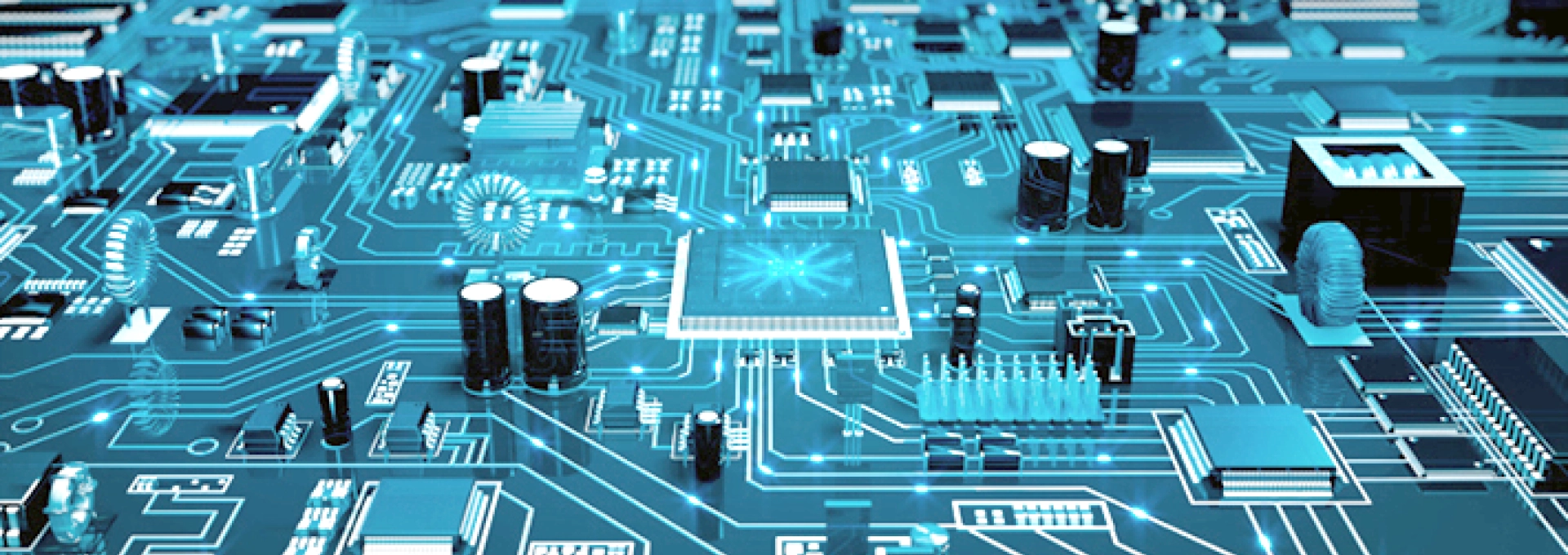
Die Miniaturisierung elektronischer Geräte schreitet unaufhaltsam voran. Dabei stoßen herkömmliche Leiterplattentechnologien zunehmend an ihre Grenzen. High-Density Interconnect (HDI) Leiterplatten eröffnen hier völlig neue Möglichkeiten für kompakte und leistungsfähige Designs. Mit ihrer höheren Packungsdichte und verbesserten elektrischen Eigenschaften revolutionieren sie die Entwicklung moderner Elektronik. Von Smartphones über Medizintechnik bis hin zur Automobilelektronik - HDI-Leiterplatten sind der Schlüssel zu innovativen Produkten der Zukunft.
HDI-Leiterplatten für verbesserte elektrische Leistung
Ein zentraler Vorteil von HDI-Leiterplatten liegt in ihren überlegenen elektrischen Eigenschaften. Durch die Verwendung feinerer Strukturen und fortschrittlicher Fertigungstechnologien ermöglichen sie eine deutlich verbesserte Signalübertragung und Leistungseffizienz.
Geringere Stromverluste durch dünnere Leiterbahnen
HDI-Leiterplatten nutzen extrem dünne Leiterbahnen mit Breiten von teilweise unter 100 µm. Diese feinen Strukturen reduzieren den elektrischen Widerstand und minimieren Stromverluste. Dadurch sinkt der Energieverbrauch der gesamten Schaltung. Besonders bei batteriebetriebenen Geräten wie Smartphones oder Wearables macht sich dieser Effekt durch längere Laufzeiten bemerkbar. Aktuelle Studien zeigen, dass HDI-Designs den Stromverbrauch um bis zu 15% senken können.
Höhere Signalintegrität durch kontrollierte Impedanz
Die präzise Kontrolle der Leiterbahngeometrie bei HDI-Leiterplatten ermöglicht eine exakte Einstellung der Leitungsimpedanz. Dies ist entscheidend für die Signalintegrität bei hochfrequenten Anwendungen. Durch die Minimierung von Reflexionen und Übersprechen können Datenraten von mehreren Gigabit pro Sekunde zuverlässig übertragen werden. Ein HDI-Design kann die Signalqualität um bis zu 30% verbessern.
HDI-Leiterplatten sind der Schlüssel zur Realisierung von 5G-Technologien und zukünftigen Hochgeschwindigkeits-Datenübertragungen.
Bessere Wärmeableitung für kühlere Komponenten
Die dünnen dielektrischen Schichten von HDI-Leiterplatten begünstigen eine effiziente Wärmeableitung. Thermische Vias und Kupferflächen können gezielt platziert werden, um Hotspots zu vermeiden. Tests zeigen, dass die Betriebstemperatur kritischer Komponenten durch ein HDI-Design um 10-15°C gesenkt werden kann. Dies erhöht nicht nur die Zuverlässigkeit, sondern ermöglicht auch höhere Taktraten bei Prozessoren und anderen aktiven Bauteilen.
Für weitere Informationen zu den elektrischen Vorteilen von HDI-Leiterplatten können Sie sich an Experten für fortschrittliche Leiterplattentechnologien wenden.
Optimierte Platznutzung mit HDI-Leiterplatten
Ein Hauptgrund für den Einsatz von HDI-Technologie ist die drastische Steigerung der Packungsdichte. Durch die Verwendung von Microvias und ultradünnen Leiterbahnen können wesentlich mehr Verbindungen auf gleicher Fläche realisiert werden.
Mehr Komponenten auf kleinerem Raum unterbringen
HDI-Leiterplatten ermöglichen eine bis zu 5-fach höhere Komponentendichte im Vergleich zu konventionellen Designs. Feine Leiterbahnstrukturen mit Breiten und Abständen von nur 50 µm schaffen Platz für zusätzliche Bauteile. Blinde und vergrabene Vias mit Durchmessern ab 75 µm ersetzen platzraubende Durchkontaktierungen. Dadurch können komplexe Schaltungen auf deutlich kleinerer Fläche realisiert werden.
Kompaktere Designs für tragbare Geräte ermöglichen
Die Miniaturisierung durch HDI-Technologie ist entscheidend für moderne Wearables und mobile Geräte. Smartwatches mit umfangreicher Sensorik oder Virtual-Reality-Brillen mit leistungsfähiger Grafikverarbeitung wären ohne HDI-Leiterplatten nicht möglich. Die Reduzierung von Größe und Gewicht eröffnet völlig neue Anwendungsbereiche, etwa in der Medizintechnik oder für IoT
-Sensoren.
Kürzere Signalwege für schnellere Übertragung
Durch die kompaktere Anordnung von Komponenten und Leiterbahnen verkürzen sich die Signalwege auf HDI-Leiterplatten erheblich. Dies reduziert Laufzeitverzögerungen und verbessert die Signalqualität. Besonders bei hochfrequenten Anwendungen wie 5G-Kommunikation oder Radarsystemen ist dieser Effekt entscheidend. Messungen zeigen, dass die Signallaufzeiten um bis zu 40% reduziert werden können.
HDI-Technologie ist der Schlüssel zur fortschreitenden Miniaturisierung elektronischer Geräte bei gleichzeitiger Steigerung der Funktionalität.
Zuverlässigkeit durch robuste HDI-Leiterplatten steigern
Neben den elektrischen und geometrischen Vorteilen zeichnen sich HDI-Leiterplatten auch durch eine verbesserte Zuverlässigkeit aus. Die spezielle Aufbautechnologie und hochwertige Materialien machen sie besonders robust gegenüber mechanischen und thermischen Belastungen.
Verbesserte Haltbarkeit bei häufigen Temperaturwechseln
HDI-Leiterplatten verwenden typischerweise hochtemperaturbeständige Basismaterialien mit niedrigem thermischen Ausdehnungskoeffizienten. Dies reduziert mechanische Spannungen bei Temperaturzyklen erheblich. Zuverlässigkeitstests zeigen, dass HDI-Designs bis zu 3000 Temperaturzyklen zwischen -55°C und +125°C ohne Ausfälle überstehen können. Dies ist besonders wichtig für Anwendungen in der Automobilelektronik oder Luft- und Raumfahrt.
Höhere Vibrations- und Stoßfestigkeit
Die kompakte Bauweise von HDI-Leiterplatten mit kürzeren Leiterbahnen und kleineren Vias erhöht die Widerstandsfähigkeit gegen Vibrationen und mechanische Stöße. Microvias haben eine deutlich höhere Zuverlässigkeit als konventionelle Durchkontaktierungen. Studien belegen, dass HDI-Designs Beschleunigungen von über 100G ohne Schäden überstehen können. Dies prädestiniert sie für den Einsatz in rauen Industrieumgebungen oder mobilen Geräten.
Längere Lebensdauer durch stabilere Verbindungen
Die präzise kontrollierten Fertigungsprozesse bei HDI-Leiterplatten führen zu gleichmäßigeren und zuverlässigeren Lötverbindungen. Gefüllte und verkupferte Microvias bieten eine wesentlich bessere mechanische Anbindung als herkömmliche Durchkontaktierungen. Langzeittests zeigen, dass die mittlere Zeit bis zum Ausfall (MTTF) bei HDI-Designs um den Faktor 2-3 höher liegt als bei konventionellen Leiterplatten.
Die erhöhte Zuverlässigkeit von HDI-Leiterplatten macht sie zur ersten Wahl für sicherheitskritische Anwendungen in der Medizintechnik, Luftfahrt oder autonomen Fahrzeugen.
Kosteneinsparungen mit HDI-Leiterplatten erzielen
Auf den ersten Blick erscheinen HDI-Leiterplatten aufgrund der aufwendigeren Fertigungsprozesse teurer als konventionelle Designs. Bei genauerer Betrachtung ergeben sich jedoch oft erhebliche Kosteneinsparungen über den gesamten Produktlebenszyklus.
Die höhere Packungsdichte von HDI-Leiterplatten ermöglicht eine Reduzierung der Lagenanzahl. Ein 8-lagiges HDI-Design kann oft die Funktionalität einer 12- oder 14-lagigen konventionellen Leiterplatte abbilden. Dies spart nicht nur Material, sondern vereinfacht auch die Fertigung und reduziert Ausschussraten.
Durch die Miniaturisierung können kleinere Gehäuse verwendet werden, was Material- und Logistikkosten senkt. Die verbesserte Signalintegrität und Wärmeableitung ermöglicht den Einsatz kostengünstigerer Komponenten. In vielen Fällen können teure Abschirmungen oder aktive Kühlungen eingespart werden.
Die höhere Zuverlässigkeit von HDI-Designs führt zu weniger Ausfällen im Feld und reduziert Wartungs- und Reparaturkosten. Studien zeigen, dass die Gesamtbetriebskosten (TCO) über die Produktlebensdauer bei HDI-basierten Geräten um bis zu 25% niedriger liegen können.
Kostenfaktor | Einsparung durch HDI |
---|---|
Materialkosten | 10-20% |
Fertigungskosten | 5-15% |
Wartungskosten | 20-30% |
Gesamtbetriebskosten | 15-25% |
Bei der Kostenbetrachtung sollten auch indirekte Vorteile wie kürzere Time-to-Market oder verbesserte Wettbewerbsfähigkeit durch innovative Produktfeatures berücksichtigt werden. HDI-Technologie kann hier entscheidende Wettbewerbsvorteile bieten.
Schnellere Markteinführung durch kürzere Entwicklungszyklen
HDI-Leiterplatten beschleunigen nicht nur die Fertigung, sondern verkürzen auch die Entwicklungszeit neuer Produkte erheblich. Die höhere Designflexibilität und verbesserten elektrischen Eigenschaften vereinfachen den Schaltungsentwurf und reduzieren die Anzahl notwendiger Designiterationen.
Moderne EDA-Tools unterstützen HDI-spezifische Designregeln und automatisierte Routing-Algorithmen für Microvias. Dies ermöglicht eine schnellere Umsetzung komplexer Schaltungen. Die verbesserte Signalintegrität reduziert den Aufwand für EMV-Tests und Redesigns. Studien zeigen, dass HDI-Technologie die Entwicklungszeit um 20-30% verkürzen kann.
Die Möglichkeit, mehr Funktionen auf kleinerem Raum zu integrieren, eröffnet neue Optionen für modulare Designs. Standardisierte HDI-Module können in verschiedenen Produkten wiederverwendet werden, was die Entwicklung neuer Varianten beschleunigt. Dies ist besonders in der Automobilindustrie oder bei IoT
-Anwendungen von Vorteil.
HDI-Leiterplatten sind der Schlüssel zur agilen Produktentwicklung und schnellen Markteinführung innovativer Elektronik.
Die kürzeren Entwicklungszyklen ermöglichen es Unternehmen, schneller auf Markttrends zu reagieren und neue Technologien früher zu adaptieren. Dies kann entscheidende Wettbewerbsvorteile in dynamischen Märkten wie der Unterhaltungselektronik oder dem Automotive-Sektor bieten.
Neben der reinen Zeitersparnis führt die HDI-Technologie oft auch zu qualitativ besseren Designs. Die erweiterten Möglichkeiten inspirieren Entwickler zu innovativen Lösungen. Die verbesserte Signalintegrität und thermische Leistung ermöglichen es, die Grenzen der Leistungsfähigkeit weiter auszureizen.
Um das volle Potential von HDI-Leiterplatten auszuschöpfen, ist eine enge Zusammenarbeit zwischen Entwicklern, Leiterplattenherstellern und Bestückungsdienstleistern erforderlich. Spezialisierte Partner mit Erfahrung in HDI-Technologie können wertvolle Unterstützung bei Design und Fertigung bieten.
Die Investition in HDI-Knowhow und entsprechende Fertigungskapazitäten zahlt sich für Elektronikproduzenten langfristig aus. Sie schafft die Basis für zukunftssichere Produkte und eröffnet neue Möglichkeiten in aufstrebenden Märkten wie 5G, autonomes Fahren oder Industrie 4.0.
HDI-Leiterplatten sind keine vorübergehende Modeerscheinung, sondern werden in Zukunft zum Standard in der Elektronikindustrie. Unternehmen, die frühzeitig auf diese Technologie setzen, sichern sich entscheidende Wettbewerbsvorteile. Die Kombination aus verbesserter elektrischer Leistung, höherer Packungsdichte, gesteigerter Zuverlässigkeit und Kosteneffizienz macht HDI zur Schlüsseltechnologie für innovative elektronische Produkte der nächsten Generation.